Enhancing Hydraulic System Reliability: Identifying and Preventing Common Failures
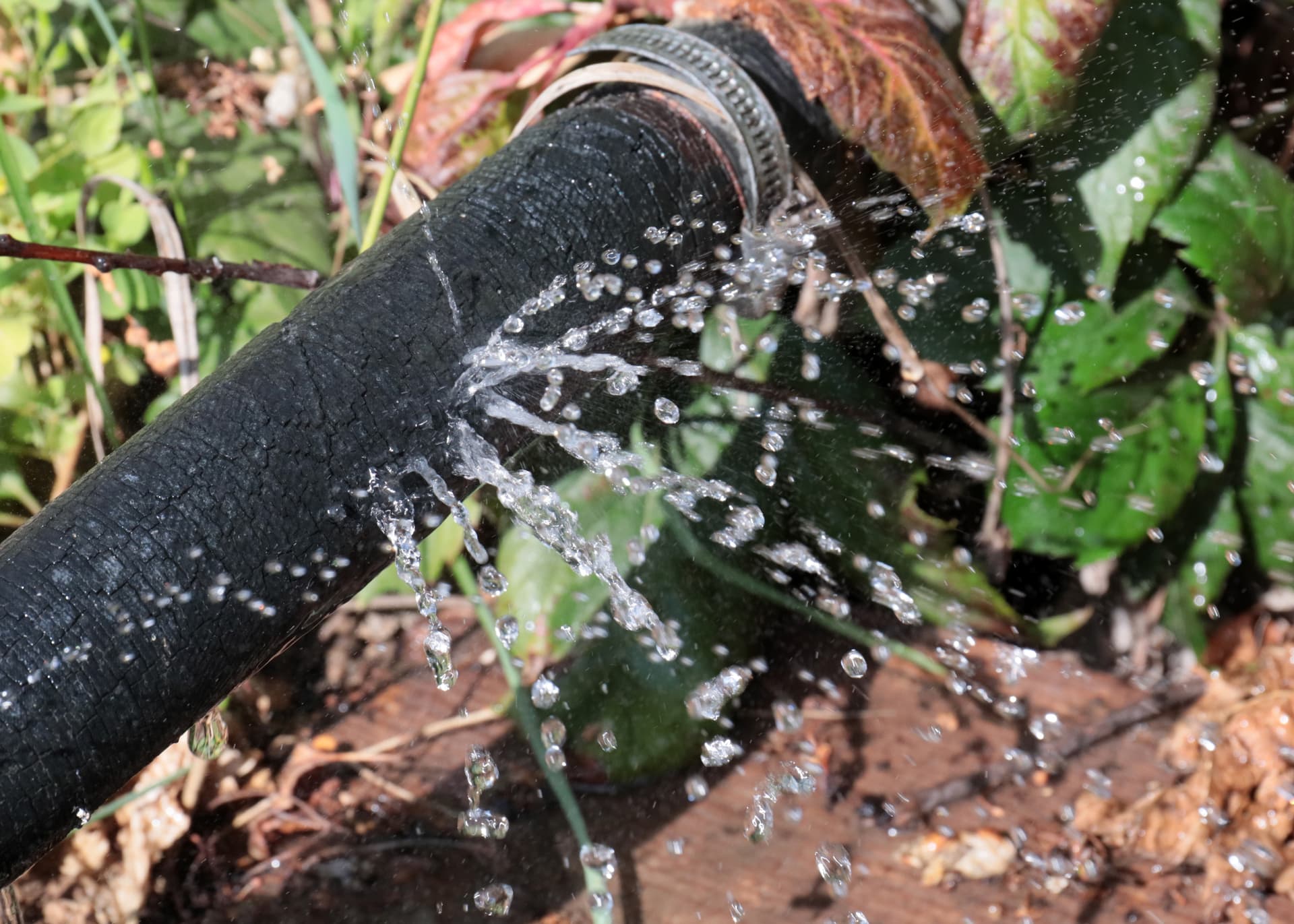
Introduction
Hydraulic systems play a pivotal role across various industries such as manufacturing, construction, aerospace, and agriculture. Despite their importance, these systems are prone to issues that can cause operational delays and expensive repairs. Recognizing and mitigating common failures can significantly improve system dependability and operational efficiency.
Key Issues and Preventative Strategies
1. Contamination: Contaminants like dirt, water, and metal shavings are major threats to hydraulic systems, entering through poor seals or during maintenance. These contaminants can cause abrasive wear, induce corrosion, and diminish the efficiency of system components. Implementing robust filtration systems, regularly replacing filters, and maintaining seal integrity are vital steps to keep contaminants at bay. Ensuring a clean workspace during system maintenance or repairs also helps in preventing the introduction of external contaminants.
2. Overheating: Excessive heat in hydraulic fluids can degrade the fluid and diminish its lubrication properties, increasing wear on system components. This often results from high ambient temperatures, overloading, or insufficient cooling. Integrating heat exchangers or coolers can aid in maintaining optimal fluid temperatures. Regular checks on fluid levels and ambient conditions around hydraulic systems are essential to prevent overheating.
3. Fluid Leaks: Leaks in hydraulic systems, often due to worn seals or loose fittings, not only decrease efficiency but also pose safety risks. Conducting routine inspections to detect and rectify leaks is crucial. Employing high-quality components and ensuring their proper installation are effective ways to reduce the likelihood of leaks.
4. Aeration and Cavitation: Aeration involves air bubbles in the hydraulic fluid, while cavitation occurs when vapor bubbles form due to low pressure. Both can cause operational noise, decrease efficiency, and damage components. Maintaining proper fluid levels and ensuring air is adequately bled from the system are preventive measures. Adjusting pressure settings appropriately can also help mitigate cavitation risks.
5. Incorrect Fluid Selection: Utilizing inappropriate hydraulic fluids can cause poor lubrication, increased wear, and issues with component compatibility. It's crucial to use the fluid types recommended by the system's manufacturer and ensure the fluid's viscosity and additives are suited for the specific operational requirements. Regular fluid testing helps maintain its quality within necessary specifications.
6. Component Wear and Tear: Components such as pumps, valves, and cylinders are subject to wear over time due to friction, pressure, and continuous use. Routine maintenance and replacing components as needed are essential to avoid system failures. Proper lubrication reduces friction and wear, while condition monitoring can detect early signs of component degradation.
7. Improper Installation and Assembly: Misaligned or improperly installed components can create excessive stress and lead to system failure. Ensuring that installation and maintenance personnel are well-trained and follow manufacturer’s guidelines can prevent such issues. Utilizing proper alignment tools and techniques during installation ensures correct setup.
Conclusion
Preventing hydraulic system failures involves a proactive maintenance strategy, careful selection of components, and strict adherence to operational guidelines. By understanding the common causes of system failures and implementing effective preventative measures, the reliability, efficiency, and lifespan of hydraulic systems can be significantly enhanced. This proactive approach helps minimize downtime and reduce maintenance costs, ensuring smoother operations across various industrial applications.